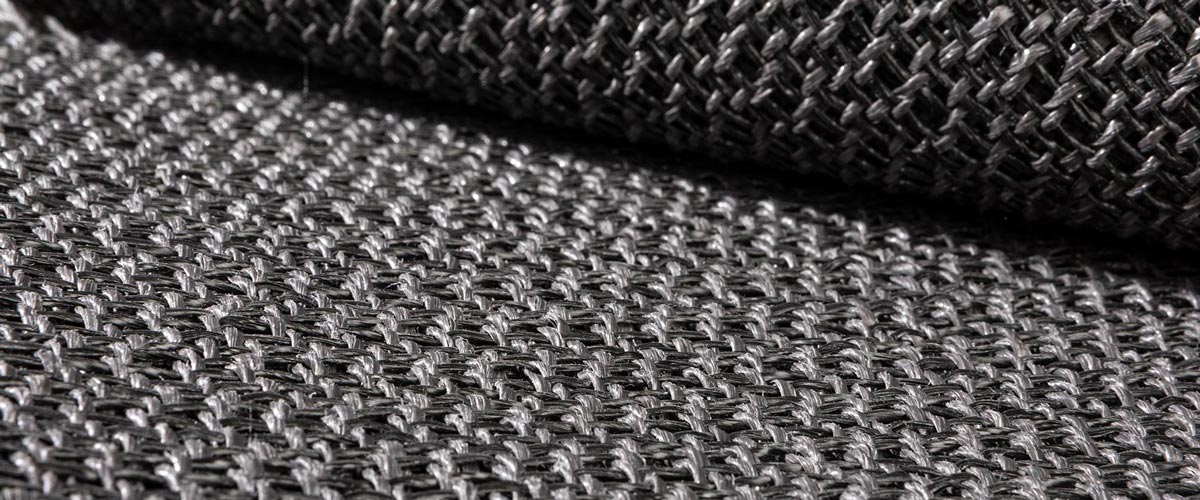
19 Nov Dewforge, James Dewhurst’s Easy-to-forge SRPP Woven Composite
James Dewhurst has marketed a new SRPP woven composite. The new product was named DewForge, as it can easily be moulded into the desired shape. DewForge will certainly satisfy customers who plan to produce more challenging thermal forms such as crash helmets, suitcases and sports protective equipment. What’s more, the fabric is lightweight and cost-effective.
ROAD TO THE DEWFORGE FABRIC
Thanks to James Dewhurst’s strong and long-time technical presence in the composite market, the company has identified a number of key growth areas in which they could develop technical fabrics. James Dewhurst’s partnership with cutting-edge raw material manufacturers and its collaboration with customers that have strong development values are of major importance for the company’s successes.
James Dewhurst has developed a patented manufacturing process that makes them the only company capable of manufacturing SRPP compound structures.
Mid 2019, DewForge was launched into the market with some key development partners. Now, the DewForge range is available to the open market in the form of our leading product DewForge 900, a 900GSM compound SRPP woven composite.
DEWFORGE
Compared to the current industry solutions, with zero delamination being the main solution, James Dewhurst’s products have many improved characteristics. Next to a reduced processing time and cost, James Dewhurst’s products have, for example, an improved impact resistance.
The DewForge fabric has been designed and developed as an answer to the increasing demand for lightweight cost-effective composites. SRPP fabrics are usually woven in flat tapes that are then layered together to produce a thermally formed panel. James Dewhurst has designed DewForge to resolve the need to layer fabrics. That way, faults in the form of air pockets are avoided and the fabric’s performance on impact resistance and delamination is increased.
Thanks to the unique way in which the DewForge fabric is produced, its users are capable of producing more challenging thermally formed shapes in one press. Those include crash helmets, suitcases and sports protective equipment.
The added benefits the DewForge fabric provides its customers when manufacturing are that the fabric doesn’t need to be layered. That benefit reduces the processing cost, as it is less labour-intensive and it reduces the heat transfer.
SALES MARKET
A multitude of industries is served, ranging from the automotive industry over luggage to protective helmets and body armours for sports and ballistics. Automotive examples are lightweight panelling and aerodynamic deflectors, while roller and carry cases are examples for the luggage industry.
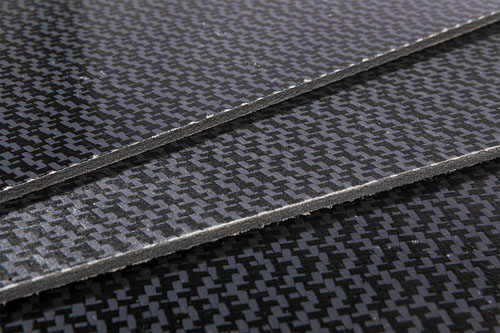